11/23/2023
Filtros de mangas e fluido hidráulico foram destaque no 2° Seminário Brasileiro de Filtros
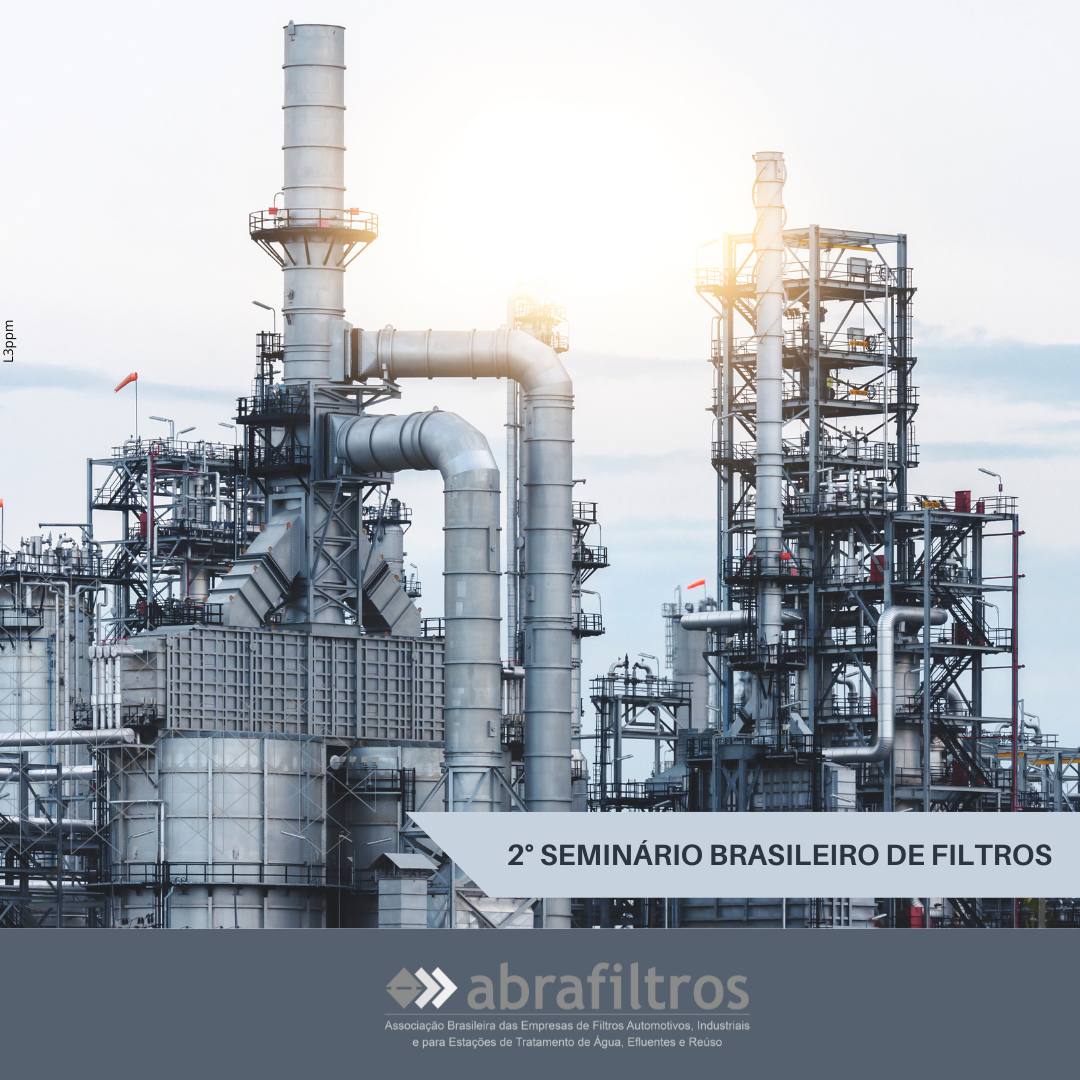
O painel de filtração industrial do evento destacou a utilização da fluidodinâmica computacional para o aumento de performance de filtros de mangas e também o controle de contaminação de fluídos hidráulicos para extensão da vida útil de componentes.
O 2° Seminário Brasileiro de Filtros, promovido pela Abrafiltros – Associação Brasileira das Empresas de Filtros Automotivos, Industriais e para Estações de Tratamento de Água, Efluentes e Reúso, realizado no dia 8 de novembro, de forma on-line e gratuita, teve programação com várias palestras sobre os segmentos de filtração industrial, residencial, ETA/ETE e reúso e automotiva, com a participação de especialistas.
O painel de filtração industrial teve início com a palestra da Profa. Dra. Sandra Mara Santana Rocha, docente do Centro Tecnológico da Universidade Federal do Espírito Santo – UFES na palestra "Uso da Fluidodinâmica Computacional para avaliar a Performance de Filtros de Mangas Industriais".
Sandra explicou que cerca de 4 milhões de pessoas morrem prematuramente em consequência da poluição do ar e 90% da população mundial está exposta a níveis de concentrações de poluentes acima do recomendado pela OMS. Os principais poluentes das grandes cidades são dióxido de enxofre, monóxido de carbono, ozônio, óxidos e materiais particulados. Os filtros de mangas tratam as partículas inaláveis finas, que trazem problemas ao meio ambiente e à saúde, pois chegam alvéolos. “A filtração de manga ocorre de forma cíclica, na primeira filtração, conforme tem incremento de materiais particulados nos tecidos uma barreira vai sendo criada com o entupimento de carga, dificultando a passagem do ar limpo e sobrecarga nos ventiladores e quando chega a um delta p máximo, ao diferencial de pressão máxima, necessita fazer a limpeza no filtro de manga”, comentou Sandra.
No entanto, após a primeira limpeza, tem um delta p residual, e parte das partículas não sai da torta e não é liberada, então o próximo ciclo será um pouco menor. “Mas, o ideal é que se maximize este ciclo de filtração e que eu não tenha que limpar tantas vezes, desgastando o tecido”, ressaltou a Sandra, acrescentando: “As partículas maiores ficam na superfície, formando uma camada sobre o tecido, e depois começa a formação da torta de filtração, passando a ser elemento filtrante de todas as partículas que chegam”.
De acordo com Sandra, a limpeza das mangas pode ocorrer de três formas: sacudimento mecânico, limpeza sônica e jato pulsante, mais usada. A de jato pulsante tem maior durabilidade das mangas. “Hoje, há estudos, inclusive, com diferentes formas de jatos pulsantes de alta e baixa pressão”, comentou.
Ela explicou que não há deslocamento da torta de forma total, o que chamam de peach cleaner (limpeza em bloco), pedaços de torta intacta que não limpou, aumentando ainda mais aquela perda de carga residual, sendo este objeto de estudo do seu grupo de trabalho. “No estudo, verificamos velocidades diferentes de filtração e percebemos que quanto maior a velocidade, maior a profundidade de penetração de partículas e menos partículas saíam na limpeza. Melhor em velocidade mais baixa, mas se reduzir muito precisará de filtro muito maior, o que seria problema na indústria”, esclareceu.
Falou também que fizeram vários ciclos de filtração para observar onde teria estabilidade de delta p, que ele não aumentasse muito no início da filtração, e se percebeu que ocorria formatação do tecido, mais rápidas para velocidades maiores e também fizeram estudo de penetração do tamanho das partículas. “Partículas menores, geralmente, penetravam mais profundas no tecido e era mais difícil de sair na limpeza”, disse. Ressaltou que não pode ter a razão ar pano muito baixa porque precisaria de grande energia, operar o filtro por mais tempo, ter maior área de filtração, e acúmulo na entrada.
Sandra contou que na fluidodinâmica computacional há o domínio computacional e malha, estudo das equações básicas, modelagem da turbulência e as condições de contorno. Os primeiros estudos dela foram iniciados em 2008 e, hoje, com a melhoria da tecnologia dos computadores, obtém-se, resultados superiores neste trabalho. “No domínio computacional e malha é onde se faz o desenho do equipamento, a estrutura que ser quer simular, a malha é um refinamento, depois vêm as equações que usamos, identificar o regime de turbulência que se vai operar e as condições de contorno que cada um destes elementos precisa trabalhar”, afirmou Sandra, ressaltando que há todo um cuidado para tirar a influência da malha e aparato construído para garantir o resultado da simulação.
Durante sua apresentação, comentou os resultados de seu trabalho, a equipe observou que a alimentação era abaixo das mangas e quiseram alimentar de outros locais. Na conclusão, observou-se que a dupla invertida teria melhor distribuição. “A entrada frontal não é boa porque as primeiras mangas pegam grande volume de massa e na lateral algumas mangas também são mais demandadas”, comentou Sandra. Também foram colocados anteparos sólidos e perfurados na entrada, melhorando o problema de pressão sobre as mangas, com destaque para o perfurado. Também estudaram a divisão do fluxo com defletoras e de vazão, sem grandes resultados.
No estudo de 2018, analisou a supressão de mangas. Algumas mangas que não eram demandadas, foram retiradas, otimizando a filtração, melhorando o tempo de filtração. “Com a fluidodinâmica computacional conseguimos estudar como acontece a distribuição do gás nos bocais de cada uma”, concluiu.
Ao final, destacou o estudo “Avaliação do escoamento no interior de um filtro de mangas industrial utilizando CFD”, apresentado no Momento Acadêmico pela aluna Julia Zucchi Vargas, Especialista em Pesquisa e Desenvolvimento na ArcelorMittal.
Em sua apresentação, Julia destacou as motivações que levaram ao estudo: melhoria na distribuição do fluxo ao longo das mangas e na eficiência de filtração, aumento da vida útil das mangas para redução de custos operacionais e beneficiar meio ambiente.
O estudo avaliou a distribuição do fluxo de gás nas saídas do duto de entrada do filtro, a distribuição do fluxo de gás nas mangas e a influência das chapas defletoras na distribuição do fluxo de gás nas mangas.
Apresentou um esquema de despoeiramento, adotado na indústria, por meio de coifas, os gases e partículas são capturados e levados por rede de dutos para equipamentos de controle, no caso filtros de mangas, que vão realizar o processo de retenção das partículas e liberar ar limpo para atmosfera. O filtro de mangas avaliado está numa siderurgia, com carros torpedos onde ocorrem reações química e liberam gases e partículas.
Usou a fluidodinâmica computacional para simular diversas condições para propor melhorias, sem necessidade de realizar testes em campo e acessando o equipamento.
Após análise, o estudo concluiu que a distribuição do fluxo de gás não é uniforme no duto de entrada do filtro. Também foi verificado que a presença de defletoras definidas no projeto resultou em menores valores de velocidade na região inferior da câmara e das mangas. Em relação à velocidade de filtração ao longo das mangas, observou-se uma distribuição não uniforme tanto com ou como sem defletoras e também que as defletoras reduziram em 6% as regiões de altas velocidades.
Controle de contaminação do fluido hidráulico e extensão da vida útil de componentes
O fluido hidráulico tem funções relevantes para o bom funcionamento dos equipamentos, entre elas, transmissão de energia, lubrificação das partes móveis, transferência de calor, vedação das folgas entre as partes, estabilidade da viscosidade, resistência à oxidação e à formação de espuma e propriedades antidesgaste. “Cerca de 75% das causas de paradas de equipamentos na indústria estão diretamente ligadas ao fluido hidráulico, 15% obsolescência e 10% acidentes”, alertou Daniel Costa, Hy-Pro Filtration Manager/Donaldson Brazil, na palestra “Controle de contaminação do fluido hidráulico e extensão da vida útil de componentes”. Citou como problemas, a degradação de superfície e mecânica, corrosão, abrasão, fadiga e adesão.
As contaminações podem ser por partículas ou poluentes sólidos, líquidos e gasosos. No caso da contaminação sólida, o dano inicial é por abrasão, que vai aumentar as folgas internas, impacto na propriedade de regulação das válvulas, perda de potência do sistema e redução da performance de bombas. A contaminação líquida dada por água, ocasionando corrosão e desgaste, alteração da viscosidade do fluido, impacto nas propriedades lubrificantes, envelhecimento do fluido e baixa filtração. Já a gasosa, provoca formação de espuma, resposta imprecisa das válvulas, perda de energia, danos à bomba, reação química com o fluido e oxidação. “Todas as contaminações acabam ocasionando redução da disponibilidade da máquina”, ressaltou.
Segundo o palestrante, a contaminação ingressa no sistema de várias formas, durante a fabricação, por carepas de solda, materiais têxteis, resíduos de jateamento/pintura e de óleo de conservação. Na operação, por desgaste das partes metálicas causadas por abrasão, desgaste das vedações, corrosão e oxidação devido à contaminação por água, produtos de desgaste do fluido e substâncias insolúveis da mistura de fluidos. Há também a contaminação externa, diretamente do ar introduzida via hastes de cilindros, filtros de ar inadequados, vedações comprometidas, aeração, vazamentos em conexões hidráulicas e ocasionada pelo abastecimento do fluido.
Tolerâncias dinâmicas – Comentou que os componentes hidráulicos têm tolerância dinâmica. No caso de partículas sólidas e desgaste por abrasão, a partícula que dá mais problema é aquela que é exatamente do tamanho da folga, pois vai travar, se for menor flutua no filme e muito maior não entra na folga. “Os três principais efeitos são alteração dimensional, aumento do vazamento interno, perda de eficiência e desgaste”, disse. No desgaste por adesão, quando a carga rompe o filme lubrificante tem o atrito metal-metal. “As superfícies soldam e é removido material como em processo de solda a frio”, afirmou. Os efeitos por desgaste por adesão são pontos de contato metal-metal, solda a frio, adesão e cisalhamento e geração de partículas duras devido ao processo de solda a frio.
No desgaste por fadiga, explicou que partículas duras que possuem a mesma espessura da folga ficam presas na folga e o processo de rachadura é iniciado. “Após vários ciclos, a trinca se espalha, a superfície falha e partículas são liberadas”, advertiu. Entre os efeitos, citou vazamento interno, deterioração do tratamento superficial e rachaduras. Já no desgaste por erosão, as partículas colidem com a superfície ou borda do componente e removem o material devido à velocidade. Entre os efeitos, pontuou: resposta imprecisa, aderência e travamento do carretel, aumento do vazamento interno e queima do solenoide.
“Ao trabalhar com fluido contaminado, ocorrerão diversos problemas com paradas inesperadas, produção, horas extras, e trabalhar assim é muito caro. Já quando há planejamento de manutenção e se consegue operar com fluido em boas condições, apesar de o investimento inicial ser mais alto, a chance de parada é muito menor, resultando num gasto menor”, enfatizou.
Durante a apresentação, falou também sobre a classificação da contaminação, citou a NAS1638, mais comum na linha de produção, embora já inativa para novos projetos, desde março de 2001, substituída pela SAE AS4059.
Destacou que o óleo novo também é uma das piores fontes de contaminação por partículas sólidas e água, já que não é fornecido em condições de uso para sistemas hidráulicos, podendo ser causa de degradação e falha prematura de componentes. “O ideal é desenvolver um plano para atingir e manter a limpeza do fluido. É mandatório que seja filtrado”, disse.
Ressaltou que os fabricantes dos equipamentos e componentes informam o grau de contaminação recomendado, mas é o limite da contaminação. Segundo Costa, aplicando sistema de filtragem eficiente, é possível estender a vida útil dos equipamentos.
“Reduzindo o grau ISO de 23/1812 para 18/15/12, por exemplo, temos redução de até 96% de contaminantes, considerando vazão de 100 l/min”, explicou.
Filtros e elementos filtrantes – Comentou que o filtro padrão é composto por cabeçote, copo, válvula by-pass ou bujão, elemento filtrante, indicador de saturação e bujão de dreno. Sobre o elemento filtrante, explicou que a razão Beta determina a eficiência do produto, razão das partículas na entrada, dividido pelas partículas na saída.
Sobre o momento para a substituição do elemento filtrante, ressaltou que é quando o ele atinge o delta p conforme o tipo de elemento e valor informado pela fabricante. “É mandatório a utilização de indicadores de contaminação, pois assim é possível saber o momento correto da troca”, alertou.
Também citou o filtro de ar, disse que o mau funcionamento dele também pode causar problemas com contaminação. Para dimensionamento do filtro de ar, o delta p (?P) recomendado é delta p = 0,01 bar, caso esse delta p (?P) não seja respeitado, pode ocorrer diminuição da vida útil do filtro de ar, aeração da bomba, espuma no tanque e trincas na solda do reservatório. Ressaltou que em ambiente com alta taxa de contaminação, esse fator deve ser considerado no dimensionamento do filtro de ar e onde concentração de umidade, considerar filtros que permitem a entrada de ar seco dentro do tanque.
Contaminação por água – Costa explicou que há três estágios: água dissolvida, aparência translucida e limpa e difícil de separar; emulsionada, gotas muito pequenas dispersas em óleo; e livre, gotas grandes de água que se depositam rapidamente.
Entre os problemas relacionados à água, citou hidrólise e oxidação; quando a água promove mudanças químicas e físicas no óleo base; aeração, quando ocorrem espuma e entrada de ar; efeitos da viscosidade, quando a água leva emulsões estáveis, viscosidades mais altas e propriedades não Newtonianas; e efeitos dielétricos, quando reduz as propriedades de isolamento elétrico do óleo.
Destacou também efeitos na máquina com os problemas relacionados com a água no óleo, como corrosão, perda do filme lubrificante, cavitação e assoreamento e obstrução dos filtros. “A água é um dos contaminantes mais comuns e prejudiciais, podendo resultar em gravura no metal (corrosão), desgaste abrasivo em componentes hidráulicos, perda de resistência dielétrica, repartição de fluidos, precipitação aditiva e oxidação do óleo e má lubrificação”, concluiu.
Sobre a Abrafiltros:
Criada em 2006, a ABRAFILTROS – Associação Brasileira das Empresas de Filtros Automotivos, Industriais e para Estações de Tratamento de Água, Efluentes e Reúso – tem a missão de promover a integração entre as empresas de filtros e sistemas de filtração para os segmentos automotivo, industrial e tratamento de água, efluentes e reúso, representando e defendendo de forma ética os interesses comuns e consensuais dos associados.
Mais informações:
Verso Comunicação e Assessoria de Imprensa
Jornalista responsável – Majô Gonçalves – MTB 24.475
www.versoassessoriadeimprensa.com.br